Guide Bar Manufacturers provide the chain saw industry
Author:admin Date:14-03-2023
Guide Bar Manufacturers provide the chain saw industry with high quality and long lasting parts that are designed to withstand the harshest conditions. Their main products are guide bars, chainsaw sprockets and chains. They have a large variety of products that are compatible with a wide range of chainsaws.
Some of the leading guide bar manufacturers include: Stihl, Husqvarna, Oregon and GB (r). They manufacture hundreds of different guide bars that are made to fit almost any popular chainsaw on the market. You can use their parts lookup tool on their website to find the right size bar for your saw.
A typical guide bar is shaped like an L, with an attachment end, a front end and a toothed sprocket inserted with its bearing into the front end. It varies in size and shape according to the model of the chain saw to which it is attached, and may have a slot and spaced holes for fastening bolts.
Most guide bars have a chain groove in the middle that allows the saw chain to slide along it. The edges of the bar are also typically hardened to help protect the chain from wear and damage while it is slipping along the bar.
The edges of the bar are a crucial part of the tool because they are often used to firmly grip a tree or other object. They have to be able to handle the forces that will come from a chainsaw and the user of the tool at the same time.
Usually, these edge rails are tempered to the hardness of 44-53 HRC. However, some regions of the bar are unhardened or have a lower hardness between the edge rails to make them easier to bend.
If the hardened edges do flex, the deflection of the guide bar may cause cracks in the hardened edge rails even when the guide bar springs back to its original shape. This can result in a lot of downtime for the harvester and will shorten the life of the guide bar.
This problem can be solved by softening a zone in the guide bar that is not exposed to the forces of bending in front of a mounting bracket. By concentrating the bending force in this region of the bar, it is not possible for the hardened edge rails to crack at the point of deflection, but the concentrated bending can cause the edges to become wrinkled and the bar to be difficult to straighten.
These issues can be avoided by adjusting the width of the softened zone and the length of the hardened zones to minimize the concentrated bending. In addition, the hardened zones should be positioned in the center of the bar rather than the edge.
Another advantage of this technique is that the bar does not need to be removed from the harvester for restraightening and therefore has a longer service life than an unhardened bar. This means less downtime for the mechanical harvester and reduced costs for the company.
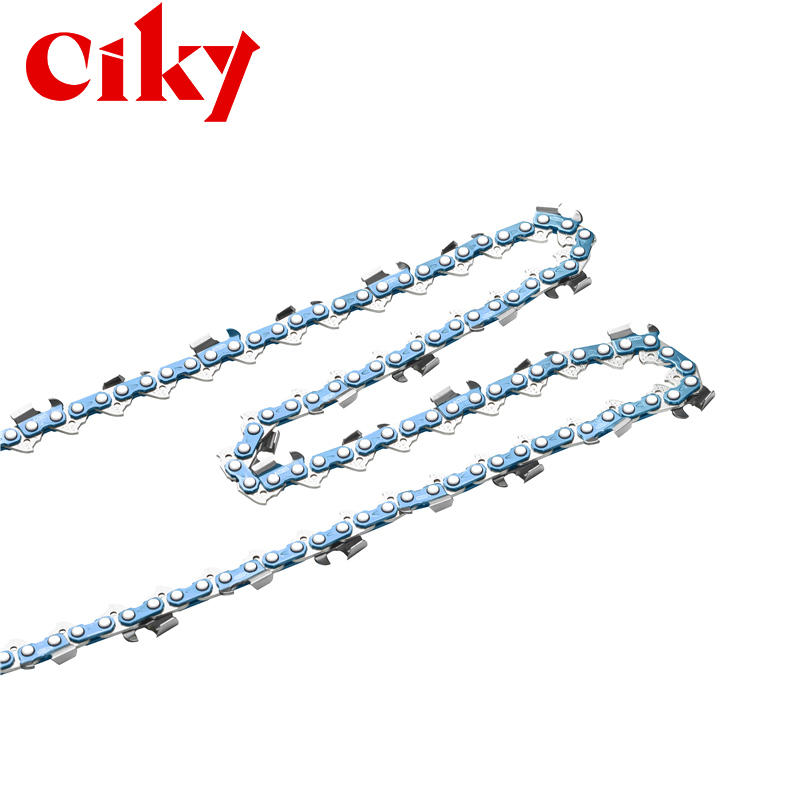